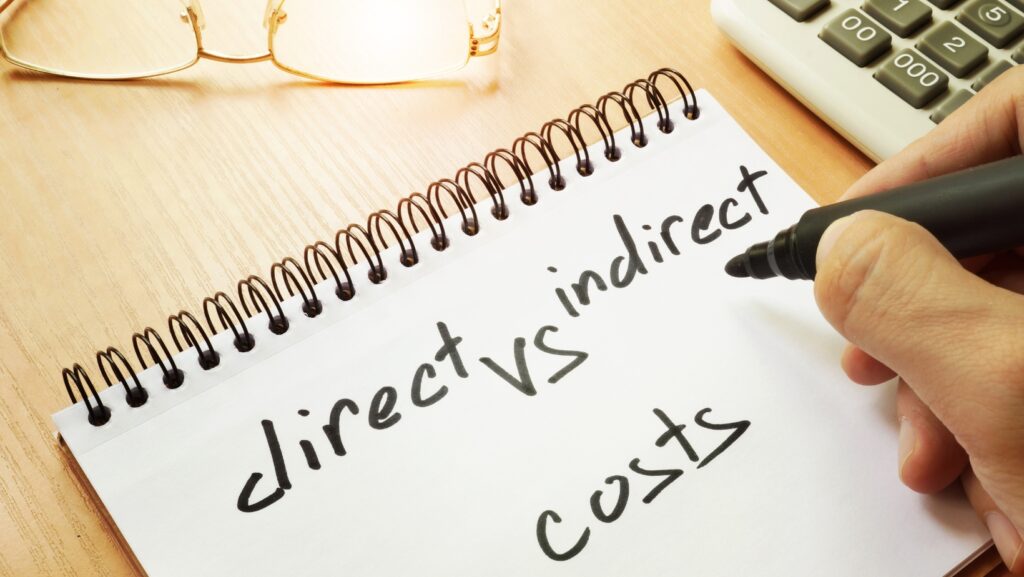
As a manufacturer, it’s important to understand the different types of costs that go into running your business. One key distinction to make is between period costs and product costs. While product costs are directly tied to the production of goods, period costs are incurred over a specific period of time and are not directly tied to the manufacturing process.
In this article, I’ll be focusing specifically on period costs for manufacturers. We’ll explore the various expenses that fall under this category and discuss why they are important to consider in your overall financial analysis. By understanding which costs are considered period costs, you’ll be better equipped to make informed decisions about your business operations and budgeting.
Which of The Following are Period Costs for a Manufacturer
Period costs refer to the expenses that are incurred over a specific period of time and are not directly tied to the manufacturing process. These costs are often associated with the overall operation of a manufacturing business, as opposed to the direct costs involved in producing goods.
As a manufacturer, it’s important to understand the different types of costs that fall under the category of period costs. Let’s explore some common examples:
- Administrative Expenses: These include costs related to the management and administration of the business, such as salaries of executives, legal fees, insurance, office supplies, and utilities. While these expenses do contribute to the smooth functioning of the manufacturing operations, they are not directly tied to the production process.
- Selling and Marketing Expenses: These costs are incurred to promote and sell the manufactured products. They can include advertising expenses, sales commissions, trade show fees, and marketing campaigns. While essential for generating sales, these expenses are not directly related to the manufacturing process itself.
- Research and Development (R&D) Costs: Manufacturers often invest in research and development activities to innovate and improve their products. Expenses related to R&D, such as salaries of researchers, cost of prototypes, and testing materials, are considered period costs since they are incurred over a specific time period and are not directly tied to the production of goods.
- General Overhead Costs: These are indirect expenses that are necessary for the overall functioning of the manufacturing business. This can include rent and maintenance costs for factories, warehouses, and offices, as well as depreciation on equipment and machinery.
Understanding period costs is essential for effective financial analysis and decision-making within a manufacturing business. These costs are not directly attributable to the production of goods and should be considered separately when assessing profitability and budgeting.
By accurately identifying and classifying period costs, manufacturers can gain deeper insights into their overall financial performance and make informed decisions to optimize their operations and profitability.
Manufacturing vs. Period Costs
Definition of Manufacturing Costs
As a manufacturer, it is crucial to understand the distinction between manufacturing costs and period costs. Manufacturing costs are expenses directly associated with the production process and the creation of goods. These costs can be further broken down into three categories:
- Direct materials: The cost of raw materials and components that go into the production of goods.
- Direct labor: The wages and benefits paid to employees who directly work on the production of goods.
- Factory overhead: The indirect costs incurred in the manufacturing facility, such as utilities, maintenance, and depreciation.
Manufacturing costs are considered product costs because they can be traced back to specific units of production. They are capitalized and included in the cost of inventory until the goods are sold.
Definition of Period Costs
On the other hand, period costs are expenses incurred over a specific period of time that are not directly tied to the manufacturing process. These costs are expensed in the period in which they are incurred and are not included in the inventory valuation. Examples of period costs for a manufacturer include:
- Administrative expenses: The costs associated with running the administrative functions of the business, such as salaries of non-manufacturing employees, office supplies, and utilities for office spaces.
- Selling and marketing expenses: Costs related to promoting and selling the products, including advertising expenses, sales commissions, and trade show participation fees.
- Research and development (R&D) costs: Expenses incurred to develop new products or improve existing ones. These costs include salaries of R&D personnel, prototyping expenses, and laboratory supplies.
- General overhead costs: Other miscellaneous expenses that are not directly related to manufacturing, such as rent for non-production facilities, insurance, and legal fees.
Period costs are reported on the income statement and are deducted from revenues to calculate the net income for a given period. While manufacturing costs are directly tied to the production process, period costs are necessary for the overall operation and management of the business.
By understanding the distinction between manufacturing costs and period costs, manufacturers can accurately allocate expenses, analyze their financial performance, and make informed decisions to optimize their operations and profitability.