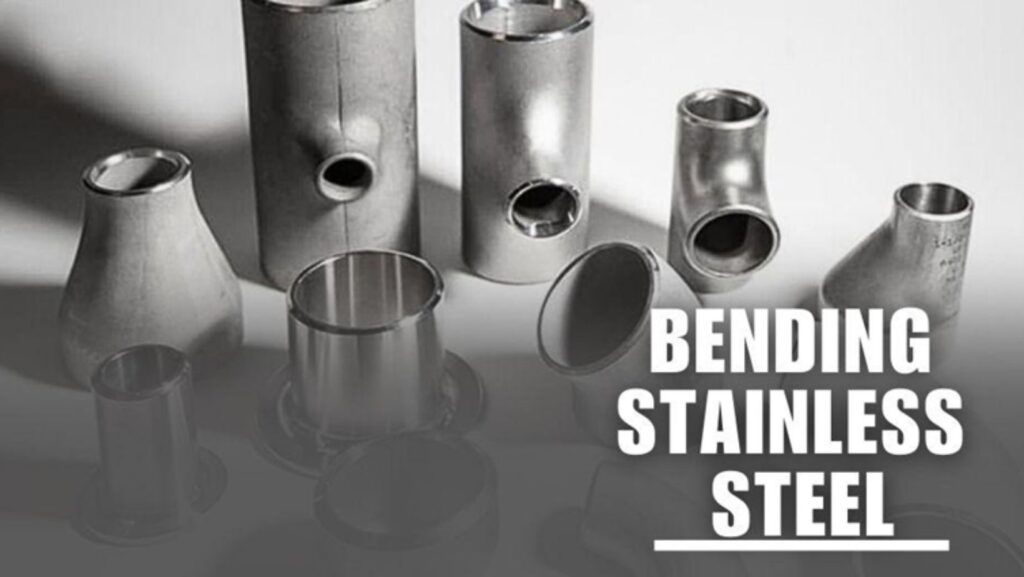
Sheet metal bending employs precise machines to form metal sheets into desired shapes. Equipment like press brakes, punching machines, ironworkers, and other presses use force on the metal. This pressure forces the metal sheet to assume a certain shape of a desired design. A few constants need to be set for correct bending, namely, the material thickness, the desired bending radius, and the K factor.
The bending process is influenced by factors like tensile strength and ductility. There are many ways of bending stainless steel. The accuracy of bending depends on the equipment choice, and the method to be used in making the measurements. Let’s explore more about bending stainless steel.
What Are the Methods of Bending Stainless Steel?
Stainless steel bending forms various shapes through appropriate techniques. The process differs based on bending radius, angle, and the material being used in the construction of the part. For accuracy, the set bending procedures are used Leading to precision. These methods guarantee the standardization of profiles and meet the project requirements.
Below are the key methods for bending stainless steel:
V-Bending
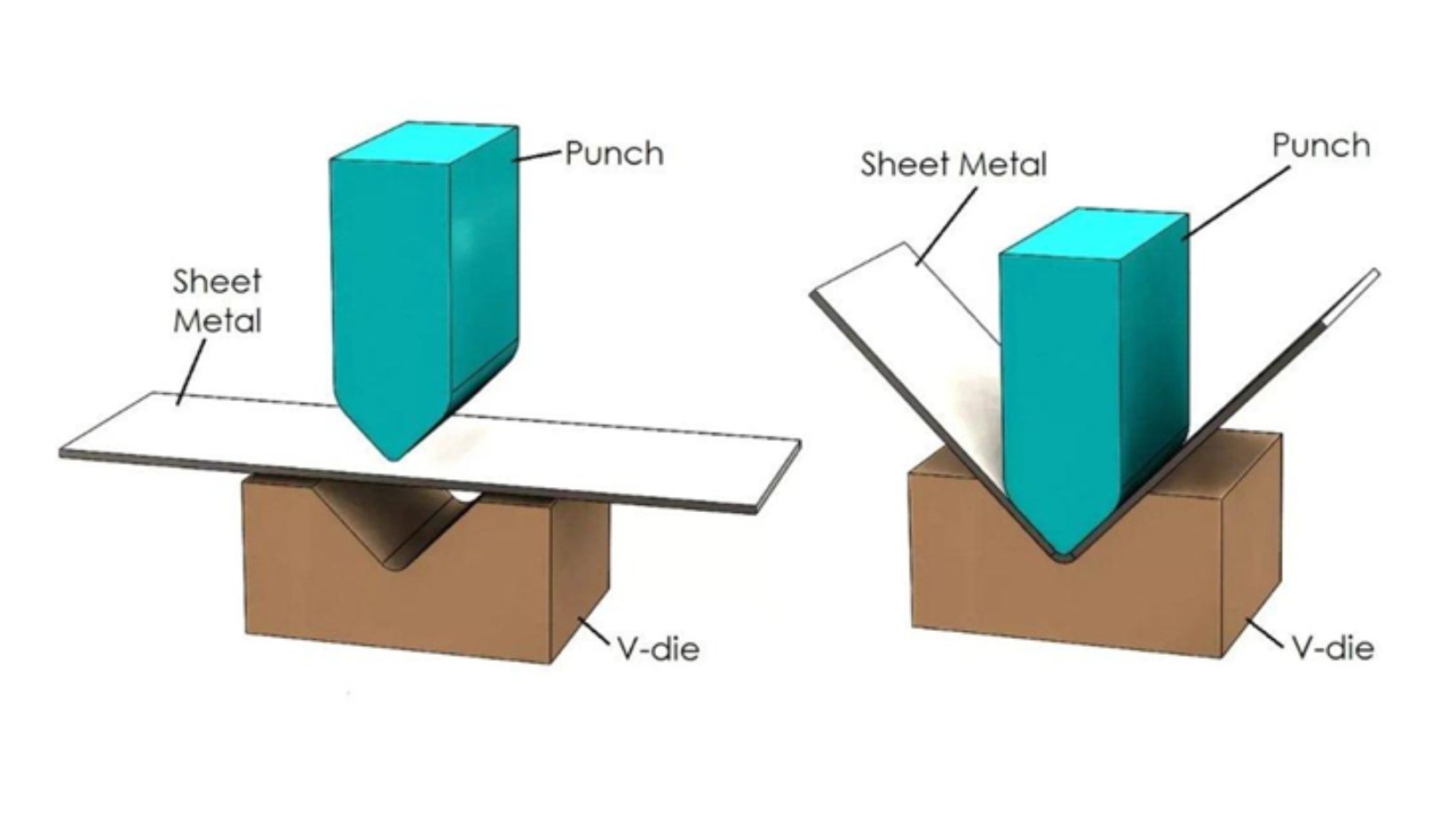
V-bending is the most preferred stainless steel bending process. In the process, a v-shaped punch and die are employed to shape the stainless sheet. The punch indents the sheet into the V-die. It also ensures precise angles, including sharp acute angles.
Roll Bending
The roll bending process is used in generating large radius curves in stainless steel. Three rolls with hydraulic power are used to slowly and progressively form the sheet. Roll bending is ideal for the extrusion of cylinders or cones and part curvatures that have similar radii.
U-Bending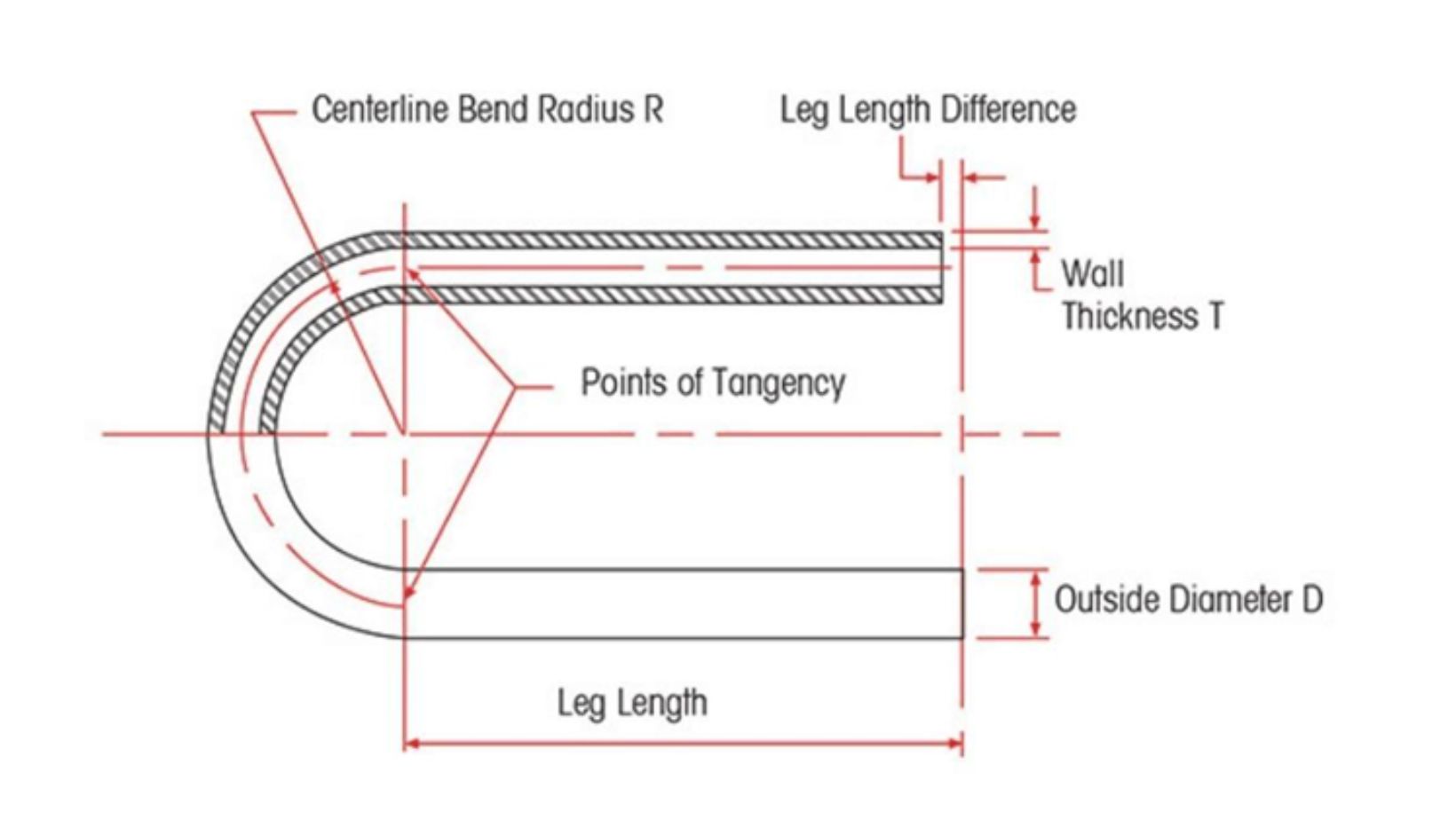
U-bending utilizes a UU-shaped die to constrain material into the shape of U-shaped profiles. The punch forces the stainless steel to produce regular bending as it presses it against the die. The service is often used for constructing a structural or decorative part.
Rotary Bending
Rotary bending provides angles greater than 90 degrees with smooth surfaces. The method uses a cylindrical tool that rotates while bending the stainless steel without sharp angles.
This method is optimum for applications that need a high surface-quality finish.
Edge Bending
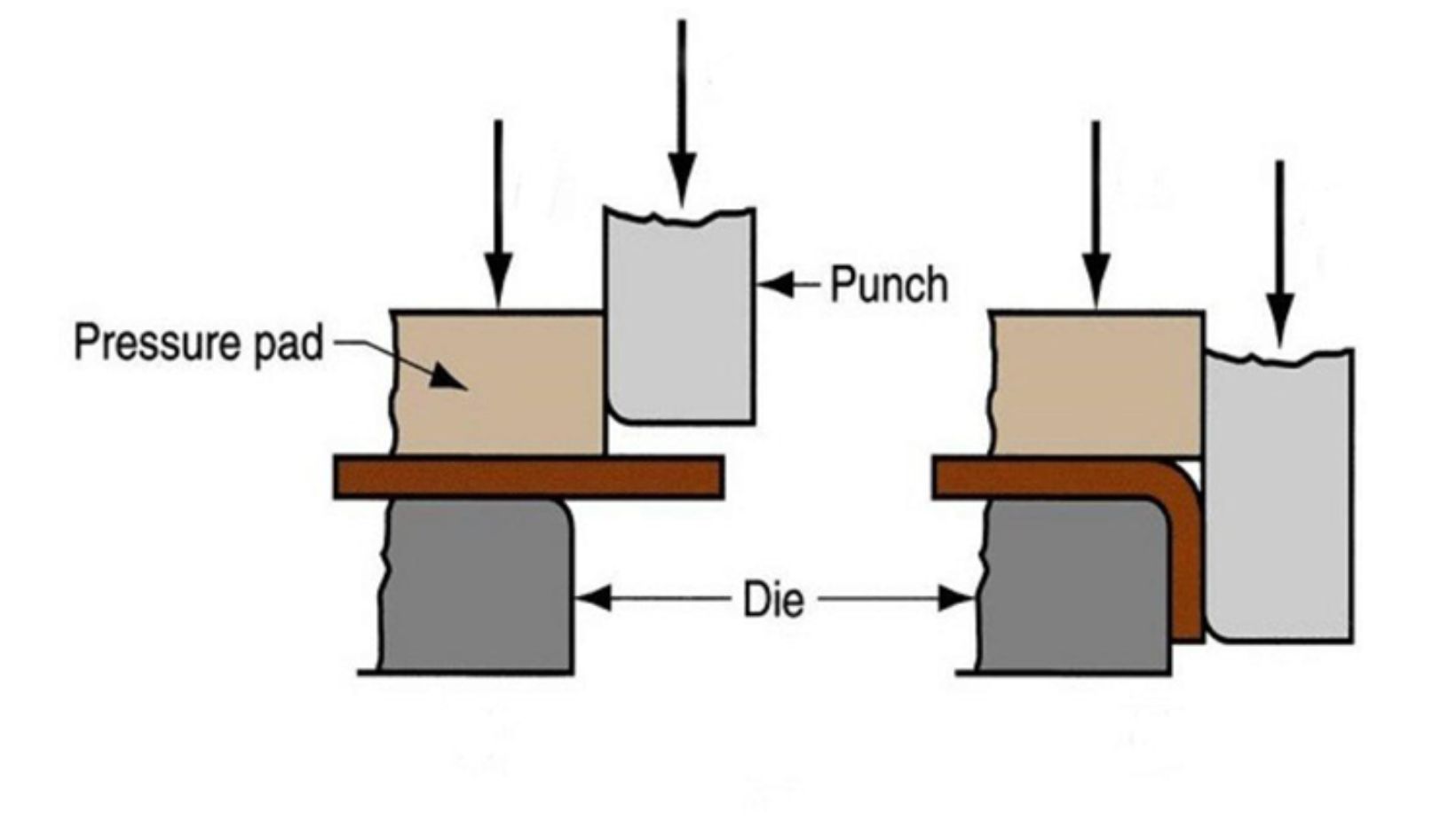
Edge bending can be applied to stainless steel panels. They use upper and lower molds, which apply pressure and flex the material. The process smooths sharp edges and works well for short sheets. All stages of long sheets should be polished carefully.
Wipe Bending
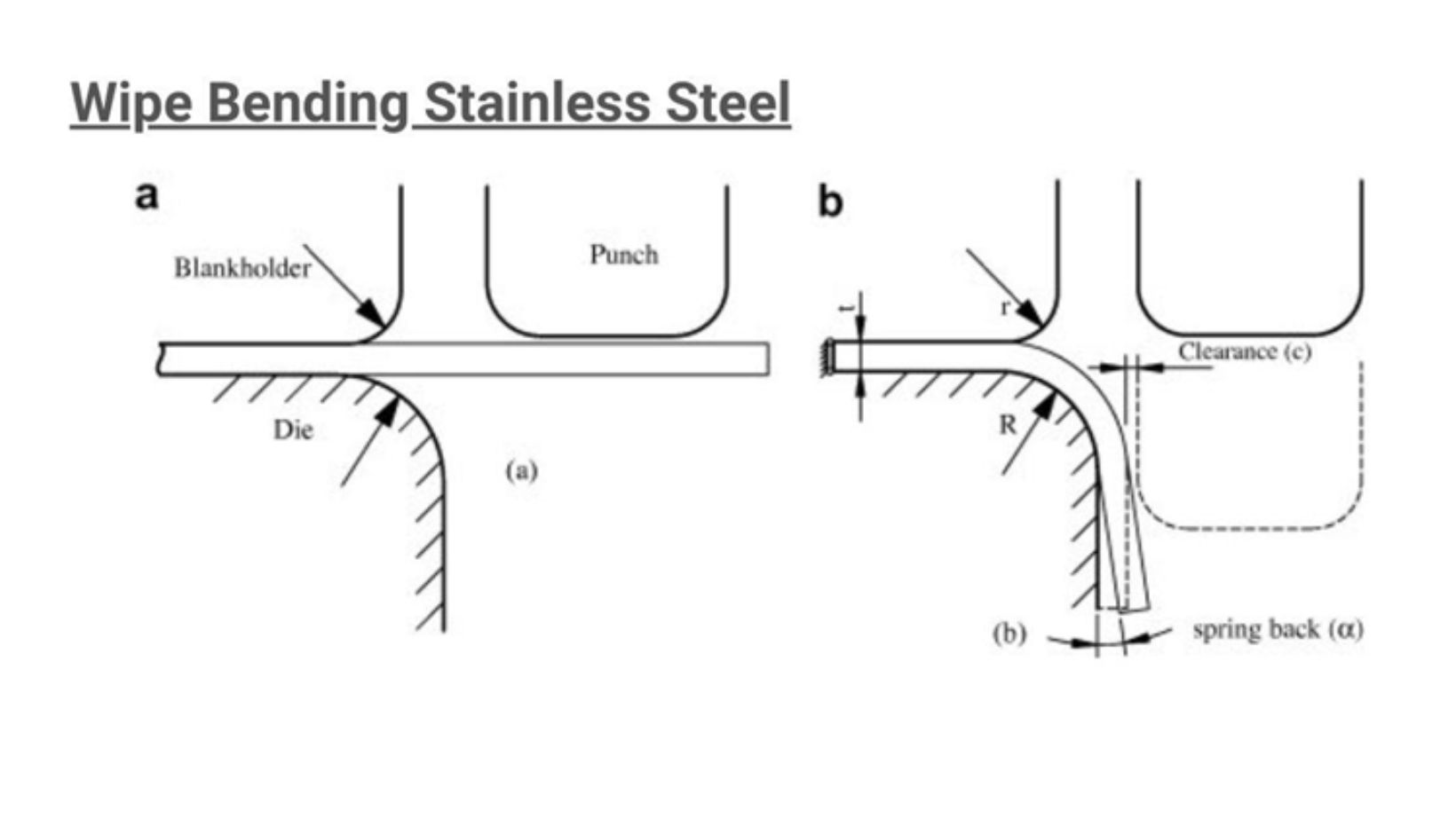
Wipe bending is used where stainless steel is placed against a lower die and then a punch and pressure pad is applied. It allows bends to be formed by shaping the edges. The method allows for closely controlled angles when welding thinner stainless steel sheets.
Bending Stainless Steel Sheet Metal
Stainless steel alloy is composed of elements such as carbon, manganese, and silicon. It is mainly categorized by carbon content: These include high, medium, low, and ultra-low emission vehicles. Stainless steel is relatively more difficult to bend than regular steel.
Since it has high yield strength and poor ductility. In addition, it results in a high spring back after bending. Therefore, it requires large bending radii to avoid failure through the formation of cracks.
Key Considerations for Bending Stainless Steel Tubing
Sheet thickness and machine force are key factors affecting impact force. Thicker stainless steel sheets need more power to bend. So, you may require a special bending machine for the accurate bending stainless steel tubing.
Bending Angle and Radius
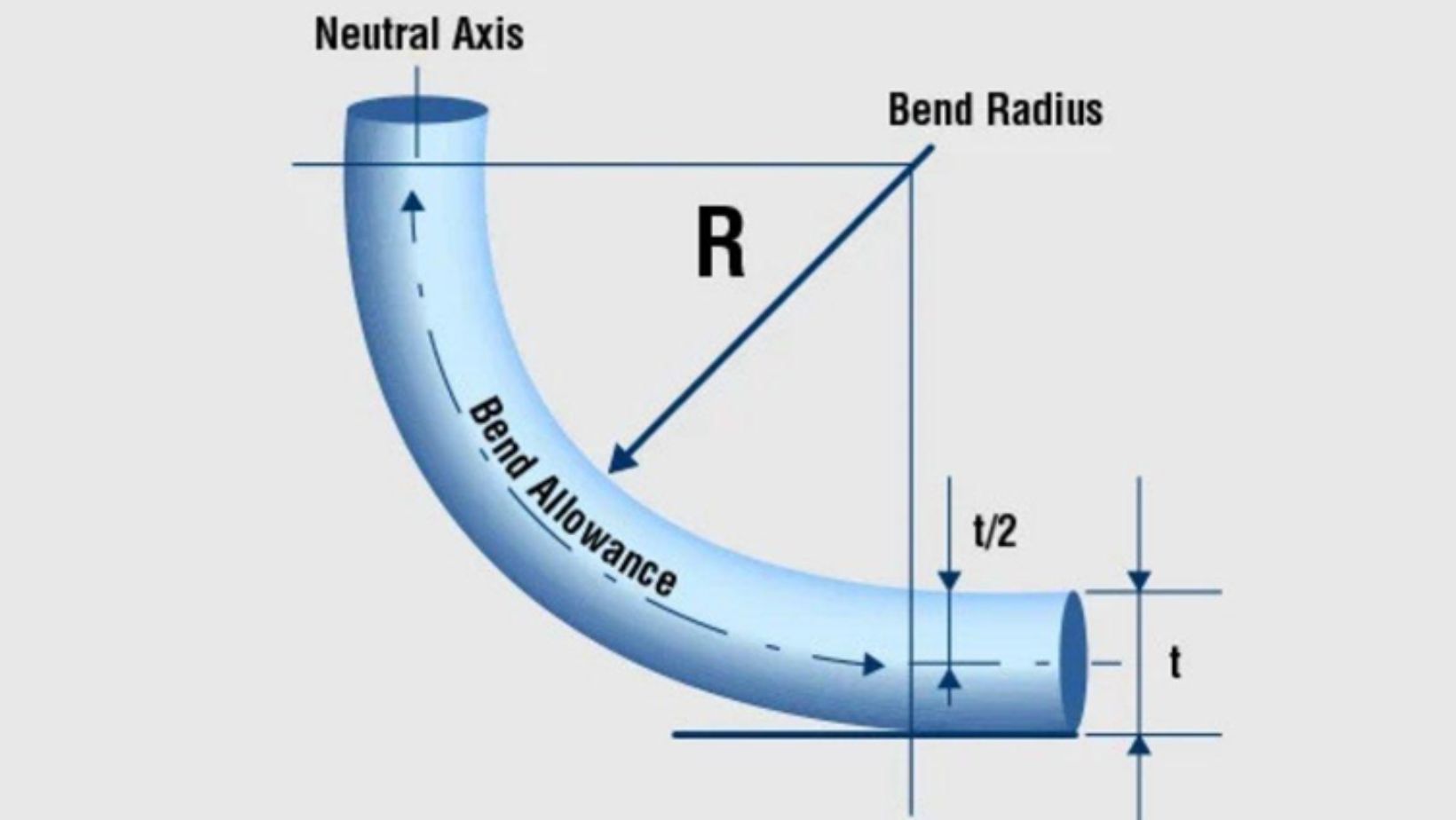
The bending angle and radius determine the degree of accuracy. A greater value tends to cause cracks, while a smaller one leads to a springback. For stainless steel, it is usually required to have a greater inner radius. Please refer to the stainless steel bend radius chart PDF for optimum quality bends.
Springback Effect
Springback rises with an elevation in the material yield strength. Stainless steel possesses a large spring back and as such requires careful setting for the correct bends to be made.
Bending Allowance
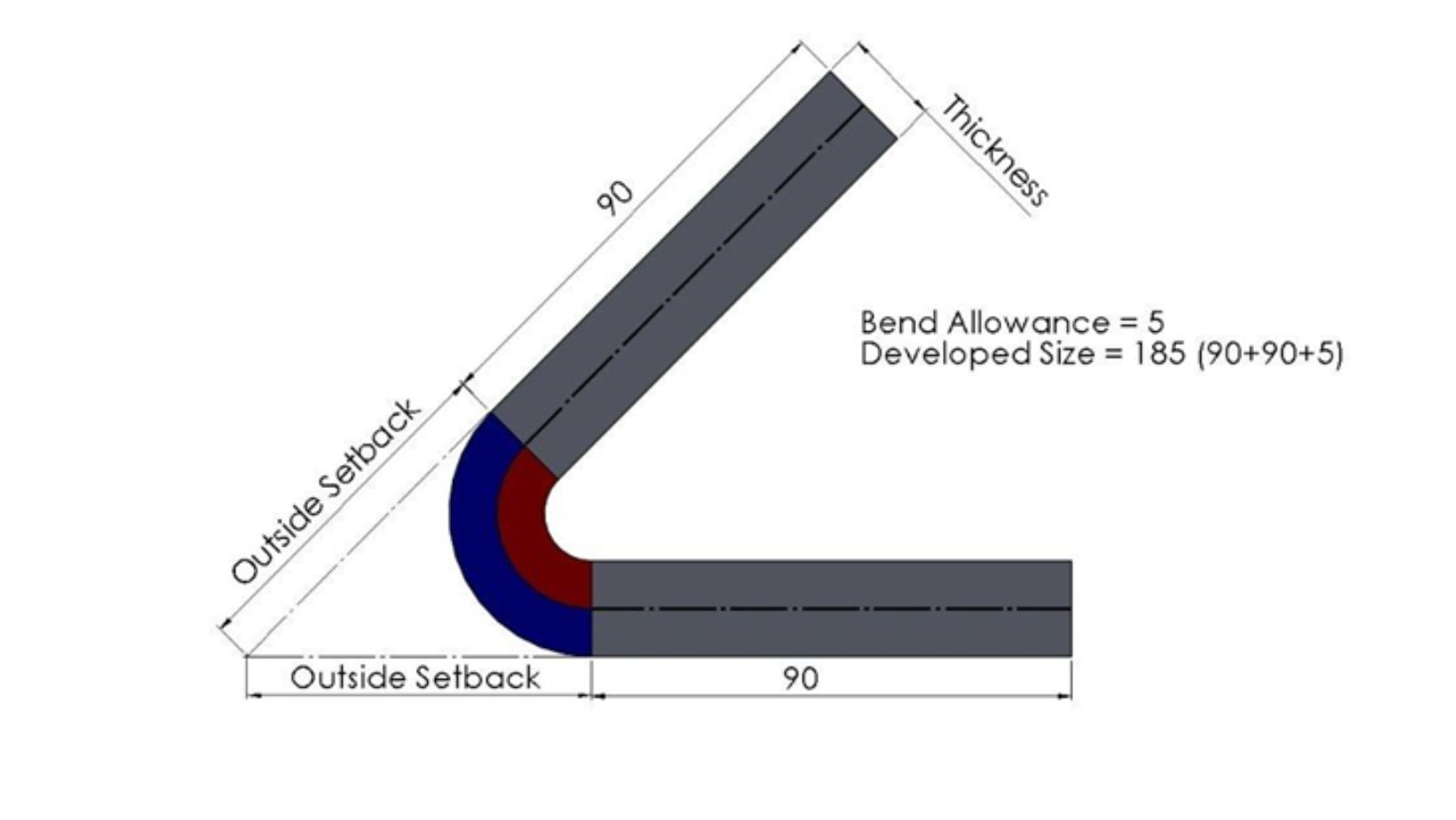
Bending allowance is used to account for the material stretch and compression on bending. It varies with the thickness, angle, and radius of the sheet.
You can calculate bending allowance by using the formula:
BA=(180π)×B×(IR+K×MT)
This accounts for the material thickness (MT), bending angle (B), inner radius (IR), and K-factor.
Annealing for Ductility
Using an annealing process, ductility can be enhanced on stainless steel. On the other hand, hot bending temperatures reduce cracking as the materials become red hot.
How to Bend Stainless Steel Without Using a Brake?
For bending stainless steel sheet metal, you may need instruments like a hammer, vise, ruler, and, protractor. Take the dimensions of the sheet thickness. Then determine the K-factor and bend allowance of the formed sheet. Draw the bending line, then use a protractor and marker to mark it. Place the sheet in the vise and then bend it with the help of a wooden hammer striking it in the middle. The use of heat may assist in bending if necessary to the metal.
Example: Bending Stainless Steel 304 Sheet
Materials and Tools
● Material: 304 stainless steel, 3mm thick, 500mm long.
● Tools: 100-ton press brake, protractor, marker, gloves, goggles.
Steps to Bend Stainless Steel
The process of bending stainless steel involves;
● Preparation: Measure and mark the sheet for the required bend.
● Calculate Bend Allowance: Use the formula of bend allowance to calculate the length of the unfolded sheet.
● Set Press Brake Parameters: Adjust the applied force and select the appropriate die type.
● Perform Bending: Place the sheet in the direction of the bend, press, and then gradually bend.
● Verify Quality: Check the angle to make sure there are no defects or cracks.
● Safety Tips: Safety glasses and gloves should be worn at all times. Organize the working environment and avoid the accumulation of building waste.
The Challenge of Bending Different Thicknesses and Stainless Steel Types
1. Thin Sheets (< 3mm)
The thin sheets of stainless steel are flexible and comparatively easy to fabricate. These are brittle and can crack if bent beyond a certain point. It’s important to control bend variation and avoid deformities.
Best Practices:
● Bend Radius: Try to retain at least 1x material thickness to minimize cracking chances.
● Springback: There is little springback, but slight overbending is done to get good accuracy.
● Tool Selection: Choose small V-die openings and minimum force to bend. Use precision tools when it comes to accuracy.
2. Thicker Sheets (3mm – 6mm in thickness)
These sheets need more energy while bending as compared to the others. The danger of a high degree of springback requires fine-tuning to ensure the desired angle.
Best Practices:
● Bend Radius: A thickness of 1.5 to 2 times the material thickness should be maintained to avoid stress on the material and consequent cracking.
● Springback: A high amount of springback is possible; determine the amount of over-bending in advance.
● Tool Selection: The press brakes should be well calibrated and force should be applied appropriately.
3. Thick Sheets (> 6mm)
Thick sheets are rigid and require a lot of force to bend. Two big issues that need specific attention are cracking and high springback.
Best Practices:
● Bend Radius: To avoid cracking it is recommended to select a bend radius of 2x to 3x the material thickness.
● Springback: Expect significant springback. Multiple strikes or adjustments are usually needed.
● Tool Selection: Use large V-die opening press brakes, preferably of heavy duty for forming.
Types of Stainless Steel Grades For Bending
1) 304 Stainless Steel
● Characteristics: The most widely used variant, it exhibits high corrosion protection and can easily be shaped.
● Bending Considerations: Moderate spring back; slight over-bending is required to achieve the desired accuracy. V-dies and punches are of standard designs which are convenient to use with calibrated equipment.
2) 316 Stainless Steel
● Characteristics: Improved corrosion performance from molybdenum for marine and chemical applications.
● Bending Considerations: High tensile strength results in high springback, thus calling for over-bending. A larger bend radius or special tools may be required in some cases.
3) High Carbon Stainless Steel
● Characteristics: These materials are difficult to fabricate and usually undergo deformation. Thus ductility increases the rate of crack formation.
● Bending Considerations: Large springback requires multiple strikes or the use of preheating. Apply a larger opening of the V-die and a greater force.
4) Low Carbon Stainless Steel
● Characteristics: More malleable Type because of higher ductility, used in the manufacturing of parts with complicated shapes.
● Bending Considerations: Low spring back results in accurate bending operations with standard tools and lower force.
Conclusion
The optimal bending of stainless steel depends on factors such as sheet thickness, material characteristics, appearance, and type of sheet to be bent. Although thin sheets are easier to fabricate, they require extra care to prevent unwanted shapes from forming. Medium and thick sheets pose much force and accurate movements to overcome the springback and cracking dangers.
Each grade of stainless steel has its features, and with the right tools, techniques, and expertise, the material can be bent accurately, achieving consistent angles.